
I don’t have any experience with Nylon at all, except the few times I have seen Professor Ganter’s graduate students fiddling with it. (FF now sells the Creator X Pro, which comes with polycarbonate panels to enclose the build space.) Though not pretty, those mods vastly improved the results of our ABS prints, and eliminated the delamination issue all together. The top is just the leftovers of the visor with a hole through it that slides around with the extruder. The rest was taken care of with a 3 dollar windshield sun visor and some spray adhesive to insulate the insides. It hangs on the heads of some longer bolts that I replaced the original screws with. One was a removable polycarbonate panel for the front sealed with some weatherstripping. With a few quick and dirty mods to the machine, we had a semi-enclosed build space that could keep our builds toasty to the finish. We had a real problem with larger prints cooling improperly, and destroying themselves by popping apart at the seams. I enclosed and insulated one of our machines. Here is what I did with our dedicated ABS printer to try to alleviate two major issues, which are delamination between layers, and warpage. Most of that kind of attitude, applied to any situation stems from frustration due to mis-understanding.
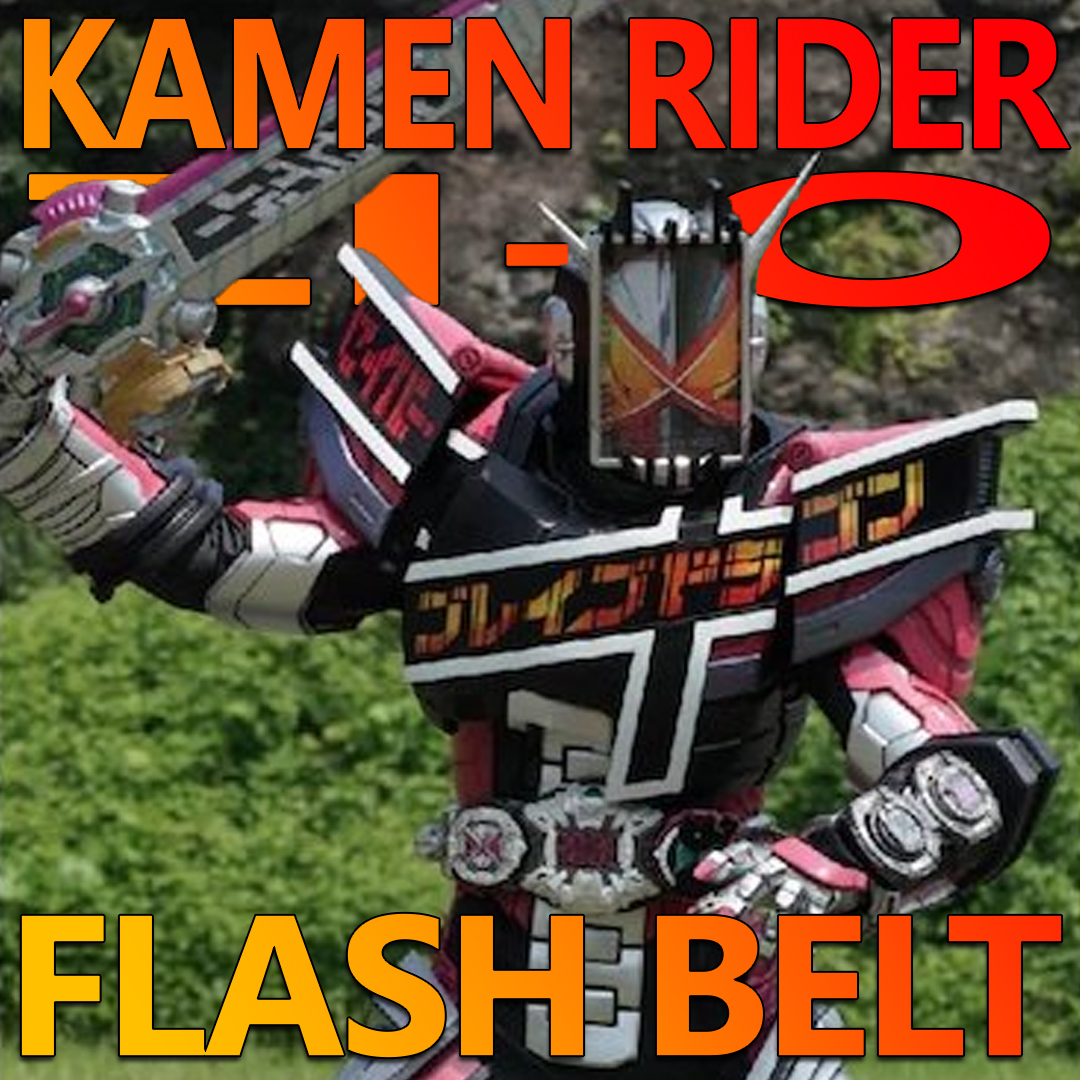
Delamination, shrinkage, pulling tape off of the bed, clogs, you name it. My mind three particular expletives were inserted in a certain order (A!B!S!) to describe my feelings about the material relative to printing it. When I first started printing with it, I was convinced that ABS really stood for something besides “Acrylonitrile butadiene styrene”.
